事例
ベテラン設計者の支援により、設計工数5%削減に成功
自動車樹脂部品サプライヤー
- ご利用サービス:
お客様の抱える問題
- プロジェクト増によるリソース不足
- 部品担当が出来る設計者が社内にいない
- メーカー(顧客)に提案できる技術者がいないため、手戻りが多く工数過多になってしまう
解決策:ご提案内容
- 自動車意匠系樹脂製品の設計経験が豊富なメンバーをアサイン
- 自社内請負チームと連携し、出図前の工数増加に対応できる体制でご支援
リソース不足、部品担当者不在、メーカーとのコミュニケーション不足から想定以上の工数負荷になっているため、可能な限り前工程で潰し込みをし、手戻り減や後工程の工数負荷減に取り組むことが効果的と考えました。
よって、樹脂の意匠系の設計経験が豊富なメンバーのアサインを通じ、設計のフロントローディング化までの提案を実施いたしました。
ポイントは、DRBFMの内容や開催頻度、顧客とのコミュニケーション回数(定例MTG)の最適化や、設計実務担当者のフォローを中心にプレイングとしてご支援いたしました。
結果
- 部品担当者として、メーカーサイドやサプライヤーに対しても豊富な知見、ノウハウを発揮し、オンスケで進捗
- 常駐サプライヤーの立場としてQCD向上を意識した設計を実施、成型性や金型要件を考慮した裏面の作り込みを提案
- 設計者解析も用い、実験/試験時の試作回数低減させることに成功
- 常駐サプライヤー主催のDRBFMにも積極的に参加し、設計フロントローディングに寄与。既存の開発工数と比較し5%の工数削減に成功
クライアントの社内で本プロジェクトのケーススタディを共有いただき、前工程での検討の重要さや設計検討事項のノウハウ共有などを通じ、クライアント社内の社員教育に活用いただけた。
設計フローの見直し等により。既存の開発と比較し5%の工数削減を実現。
自社請負支援によりクライアントの一時的な負荷低減に貢献。社員様の稼働時間20h/月・人の削減に成功。
使用した技術
意匠(デザイン)、樹脂(インジェクション成型)、製品、CATIA-V5
お客様の声
このプロジェクトの担当者
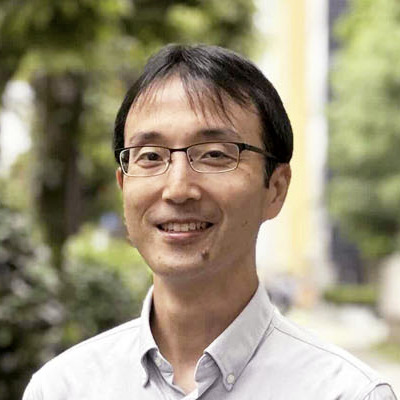
設計担当
部品主担当として、DRBFM、設計検討、DR、試験評価立ち合い、生準支援まで実施
カーメーカーさんでの経験があるエンジニアが対応していただいている為、カーメーカー目線での指摘・提案をいただいており非常に助かっています。おかげ様で出戻りも少なくなりました。